SERIALNINE technologies
Relentless innovation drives SERIALNINE, utilizing state-of-the-art 3D scanning, CAD, 3D printing, 5-axis CNC machining, and FEA testing to develop superior automotive solutions that redefine performance
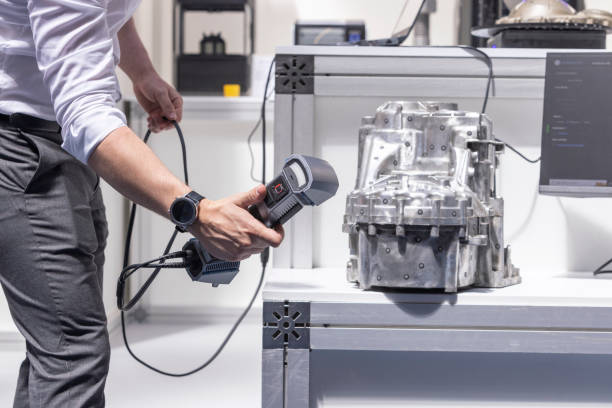
3D Scanning
Our company uses 3D scanning technology to optimize the design of our products, capturing precise measurements from OEM parts to create high-resolution digital models.
This allows our engineers to refine and ensure compatibility, enhancing performance and reducing errors typical of traditional methods. The integration of 3D scanning accelerates our design process, enabling faster market delivery and better meeting our clients' customized needs with improved quality and efficiency.

3D PRINTING
At SERIALNINE we utilize 3D printers to create precise and detailed prototype parts that provide us with a tangible model that we can use for test fitting.
This allows us to identify and rectify any design flaws or inconsistencies before initiating full-scale production runs. By doing so, we ensure the efficiency of our production process, minimize waste, and maintain the high quality of our final products. This innovative approach underscores our commitment to leveraging cutting-edge technology to enhance our manufacturing processe
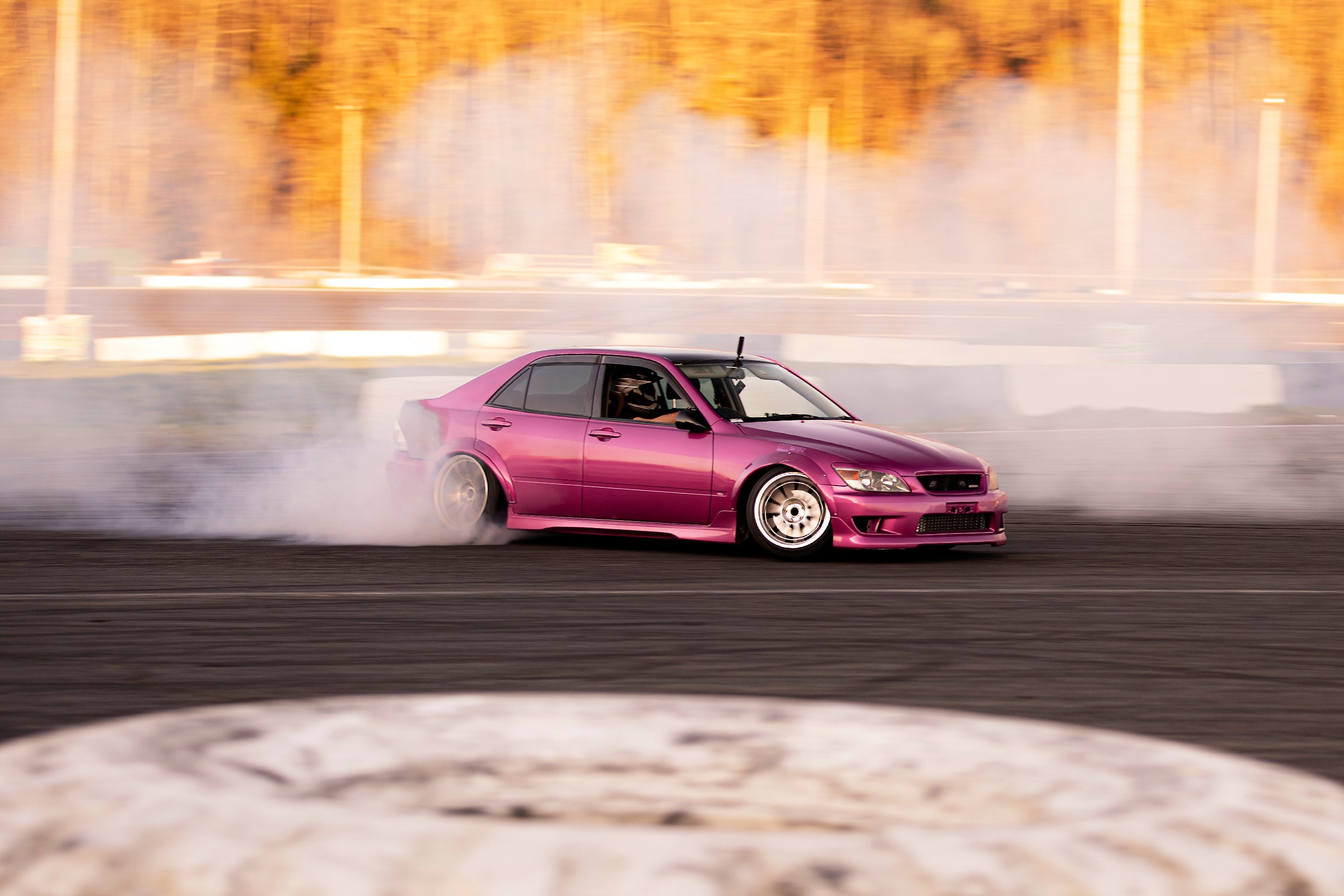
testing
Our company is dedicated to the highest quality and performance of our aftermarket suspension components.
We rigorously test our products on the street, race track and through virtual simulations to ensure durability, stability, and performance.
Real-world testing and advanced simulations help us refine designs and identify potential issues early, saving time and enhancing reliability. This dual-testing approach guarantees that our suspension components meet stringent standards, providing our customers with dependable, high-performance products.
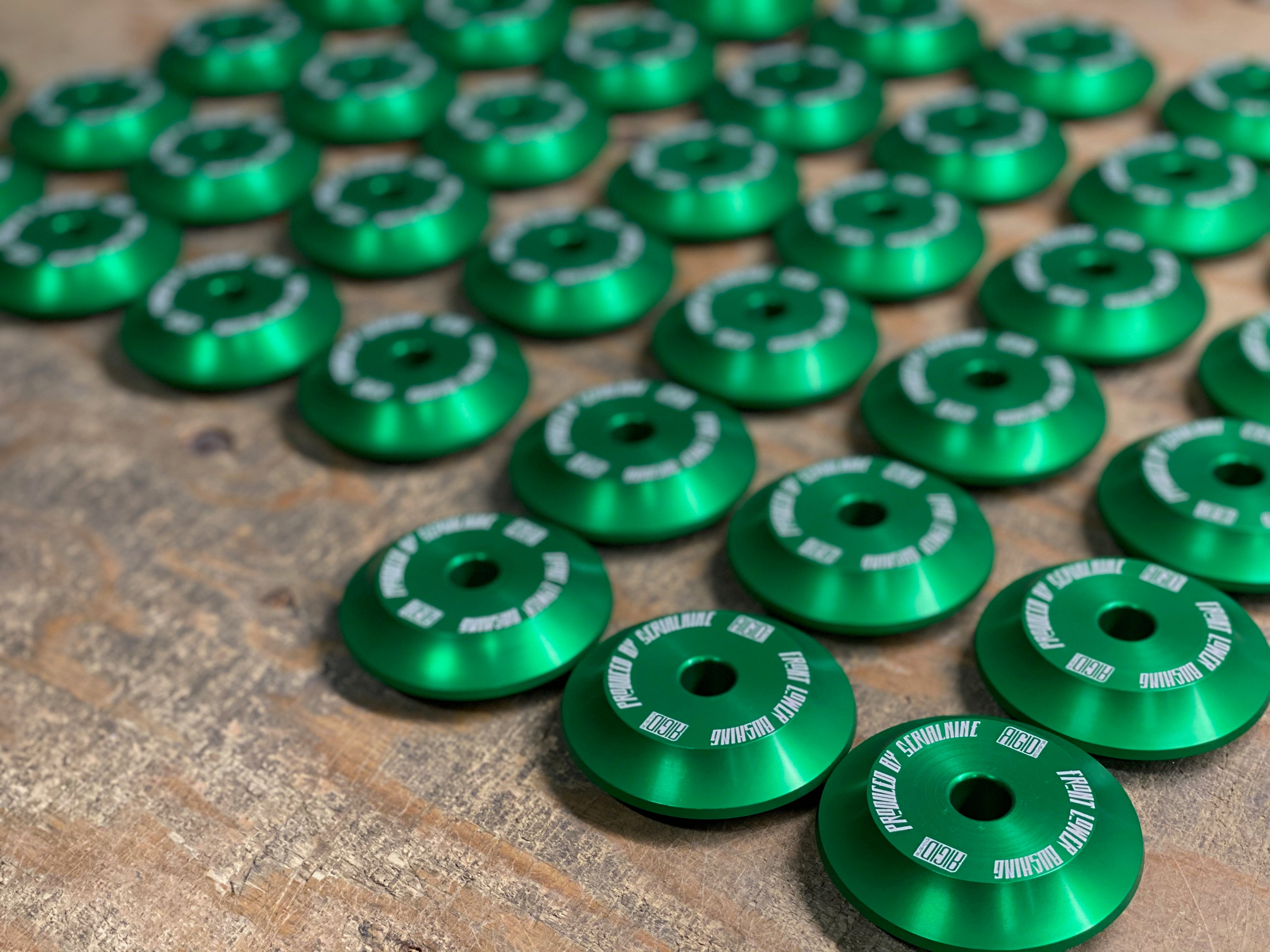
Manufacturing
We utilize advanced CNC technology, including 5-axis precision, to craft our products, enabling highly accurate cuts and complex shapes for optimal fit and performance.
Utilizing 6000 and 7000 series aerospace-grade aluminum for its superior strength and corrosion resistance, we enhance the durability of our products.
Complementing our state-of-the-art manufacturing, we collaborate with high-quality local and global partners, ensuring each component meets our stringent standards. This strategic partnership approach allows us to source the best materials and techniques worldwide, setting industry standards in quality and efficiency while maintaining reliable supply chains.

billet advantage
Our CNC billet aluminum suspension components outperform competitors’ stamped steel or welded steel tube constructions in several ways.
The precision of CNC machining ensures consistent, high dimensional accuracy, eliminating weak points often found in welded joints. Being lighter than steel, billet aluminum reduces unsprung weight, enhancing vehicle handling and fuel efficiency. Additionally, aluminum’s corrosion resistance ensures the longevity of our components. Therefore, our CNC billet aluminum suspension components offer a more robust, reliable, and high-performance solution than traditional steel counterparts.